トヨタになれなかったボーイングの過ち
(2013年1月21日 Forbes.com)
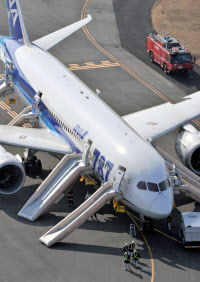
私が最近書いた「ボーイングの失敗:経営者が学ぶべき7つの教訓」(末尾の「参考文献」参照)という記事は、鋭く熱のこもった議論を引き起こした。コメントを引用した人たちの何人かは、一般的な教訓に加え、ボーイングがアウトソーシング(外部委託)と海外移転で、ある特定の過ちを犯したと指摘した。それらの過ちの内容をもう少し詳しく精査してみたいと思う。
ボーイングはこれまで、米国内でも海外でも、コスト削減と製品開発の加速を目的として、アウトソーシングに特に力を注いできた。こうした方針により「787型機の開発期間を6年から4年に短縮、開発コストを100億ドルから60億ドルに削減する」ことが狙いだった。
結果は正反対になった。同機の開発費用は予算を何十億ドルも上回り、期間は予定より3年遅れた。ボーイング商用機部門の責任者、ジム・アルバウ氏は2011年1月にこう語った。「中枢の技術を本社周辺に残していた場合に比べ、ずっと多額の費用を要した」
■正しかった目標
まず、ボーイングが実行した正しい措置の話から始めよう。1990年代後半にエアバス(EADS所有)にシェアを奪われた後、ボーイングは既存機種のコスト削減(および販売価格の引き下げ)に注力することもできた。それは無情だが会社を末路に導いていただろう。ボーイングが立派だったのは、その代わりに顧客にとっての付加価値のある新型機を開発し、収益の向上を目指すと決めたことだ。
まず、同社は究極の顧客、つまり乗客にとって旅の質の向上を目指した。既存機に使われていた素材(アルミ)に代わり、新型の787型機に複合素材(カーボンファイバー、アルミ、チタン)を使うことで、客室の湿度は上昇し、気圧は一定に保てるため、空の旅の快適さは大きく改善する。軽い複合素材によって、787型機はどの2都市間でも、途中で経由地に降りることなく航行できる。
第2に、ボーイングは複合素材と、リチウムイオン電池を電源とする電気系統を使うことで燃費向上を図り、もっとも身近な航空会社により大きな価値を提供しようとした。この結果、同等機種によるフライトに比べて燃費は20%向上し、1座席・マイル当たりの運航コストは他のどの航空機よりも10%低下する見通しだった。それにもまして、既存のアルミ製だと胴体がさび、疲労も起こるが、複合素材を使用した787型機ならメンテナンスや機体交換のコストも削減できる。
ボーイングが機体の供給さえできれば、いいことずくめの内容だ。顧客たちも、ボーイングなら心配ないと判断したのは明らかだ。こうして、787型機は航空史上、最も売れた旅客機となった。ボーイングの株価は上昇し、経営陣はボーナスを得た。しかし、現実は厳しかった。
■バッテリーの過熱問題
787型機のリチウムイオン電池が危険な水準まで過熱するという現在の事象の原因が、小さな修復可能な製造上の欠陥なのか、この新型機の存続を危ぶませるような深刻な設計ミスなのか、今のところ分からない。
同社の最高経営責任者(CEO)、ジェイムズ・マクナーニ氏が金曜日、同社社員に宛てた文書で述べたように、「15カ月前に運航を開始して以来、787型機は8つの航空会社で1万8千回のフライトをこなし、フライト時間は5万時間にのぼる。世界中の目的地に100万人以上を運んだ」のは事実だ。しかし、こうした実績も、同社がリチウムイオン電池の過熱問題の真相をはっきりさせない限り、空しく響く。
今はっきり言えるのは、ボーイングが米国内および国外で実施してきたアウトソーシングでは、すでに顕在化してしまったような、あらかじめ予期されていたコストやリスクを軽減あるいは除外する手はずをとっていなかったということだ。
アウトソーシングでは、たとえ個別には確立した技術であっても、航空機を組み立ててみたら、部品どうし相性が悪かったということが起こりえるので、大きなリスクがある。「こうした根本的な問題を最小限に抑えるにはどうしたらいいのか」。ボーイングの航空機エンジニア、L.J.ハート―スミス博士は2001年に発表した大変すばらしい論文(参考文献参照)で以下のように記している。「元請けメーカーは現場の品質を維持し、部品供給元を管理、時には技術支援もする必要がある。そうでなければ、元請けは、各供給元の部品の最低限の能力を超えた製品を作ることはできない。こうしたコストは仕事の内容を目にできないだけに、無くなりはしない」
ボーイングは部品供給会社に対するこのような現場での支援体制を確立しようとは考えなかった。実際、同社はそうした責任を下請け企業に丸投げした。下請け企業がしかるべき水準の体制を組めなかった場合、ボーイングはいずれにしても技術支援に乗り出さねばならなかった。「ボーイングは787の開発遅れにつながった様々な技術的課題を解決するために、世界中のTier-1、Tier-2、あるいはTier-3クラスの部品会社にも何百人というエンジニアを送り込んだ。結局、ボーイングは航空機の部分組み立ての工程を丸ごとやり直さなければならなかった」。その結果どうなったか。巨額の追加コストが発生した。同社がもともとプロジェクトのコストとして計上しておくべきだったものだ。
■革新的技術に伴うリスク
787に盛り込まれた技術は、アウトソーシングされた実証済みのものだけではない。同型機には他のどの航空機でもまだ試されていない革新的な重要技術も採用された。カーボンファイバーの複合素材は国際線の運航という過酷な環境に耐えるのか? 過熱しやすいという悪評がつきまとい、消火が困難な火事を引き起こすリチウムイオン電池は、果たして安全に使えるのか? 誰も自信をもって答えられない。787はまた、複雑な新型の電気系統、および出力・配電パネルを搭載している。いっせいに導入された新技術による相互作用が、技術革新に伴うリスクを一気に押し上げた。
イノベーションがもたらすリスクをあえて取り込むということは、航空機の開発や生産段階でボーイングがより深く関与しなければならない意味合いを持っていた。ところが驚くべきことに、ボーイングは浅い関与にとどめ、詳細なエンジニアリングや調達を下請け任せにすることを選んだ。その結果どうなったか? 想定外の問題が絶えず発生し、開発・生産計画は延期を余儀なくされ、コストも膨らんでしまった。
■アウトソーシングのリスク
航空機のような複雑な製品を作るには、どうしても一定のアウトソーシングが欠かせない。というのも、メーカー単独ではエンジンや航空電子工学に関する専門的ノウハウを持ち合わせないからだ。しかしながら、ボーイングは787の製造にあたり、アウトソーシングの割合をそれまでの機体より大幅に増加させた。737や747型機ではアウトソーシング比率は35~50%だった。ボーイングはこれを787に関しては70%まで高めようとした。
ボーイングは外部委託を必要悪とは見なしていなかった。それどころか、他の米国企業と同様、787の開発にかかるコストと期間を削減するために、熱心にアウトソーシングに取り組んだ。「787のサプライチェーンは製造・組み立てコストを低く抑えつつ、ボーイングのサプライヤーに財務上のリスクを分散するように考えられた」
ハート―スミス博士は先ほど触れた2001年の論文で、大規模なアウトソーシングが引き起こす追加的なコストやリスクについて警鐘を鳴らしていた。同氏はこう指摘している――アウトソーシングはコスト削減や収益向上はもたらさない。収益とノウハウがサプライヤーに流出する一方、母体メーカーはコスト増に直面することになる――と。「アウトソースされるのは仕事だけではない。その仕事に付随する利益のすべてが、外部に流れ出るのだ」
ハート―スミス氏は、購買の決定は、徹底したコスト評価に基づくべきだと指摘する。「購買の決定は、製品の仕様が固まり、関連するコストがはっきりするまで、なされるべきではない」
アウトソーシングをするには、主要な組み立て部品が最終組み立て段階でうまく合わないといった事態を避けるため、通常よりかなりの労力を要し、コストは業務分担とは無縁の状態で設計した場合に比べ、格段に増える。
ボーイングはハート―スミス氏の警告に従わず、製品の仕様が固まり関連コスト計算が終了するよりはるか前に、エンジニアリングと機体製造を外部に委託することに決めた。この結果は惨憺(さんたん)たるものだ。ボーイング787のプロジェクトは、予算を何十億ドルも上回った。機体納入時期は、少なくとも7回延期された。最初の納入は計画より3年以上遅れてからだった。
■多層構造のアウトソーシングに潜むリスク
ボーイングは新しい技術の導入とともに、新しいアウトソーシングの手法を選んだために、リスクはさらに増幅した。ボーイングの従来機では同社がサプライヤーの各部品をとりまとめ、組み立てを担うという伝統的な役割分担があった。しかし、787ではサプライチェーン自体が多層構造となった。これにより、ボーイングはTier-1と呼ぶおよそ50社の取引先との戦略的パートナー関係を構築するようになった。こうした戦略的パートナー企業はそれぞれ「インテグレーター」となり、Tier-2あるいはTier-3クラスのサプライヤーが納入する部品や部位の組み立てを任された。
当然のなりゆきだが、以前にハート―スミス氏が予測していた通り、ボーイングは、Tier-1クラスの戦略的パートナーの一部が、航空機の異なるセクションに関する開発ノウハウを持ち合わせなかったり、Tier-2企業を管理し切れないことを悟ることになった。開発プロセスを立て直すため、ボーイングはTier-1サプライヤーの1社、Vought Aircraft Industries の買収を強いられるとともに、ほかのサプライヤーにノウハウを提供しなければならなくなった。ボーイングはまた、戦略的パートナー企業に対して製造の遅延に伴う損失の穴埋めもしなければならなかった。
■とってつけた「トヨタ方式」
ボーイングのアウトソーシングの手法は、トヨタが開発期間を短縮しながら新車を製造する原動力となったトヨタ方式のサプライチェーンを部分的に取り入れている。トヨタは製造する自動車の70%ほどを、信頼関係を築くグループ会社に外部委託し成功を収めている。
しかし、ボーイングはトヨタ方式のアウトソーシングの核心部分を採用していない。トヨタは、自動車全体の設計とエンジニアリングはがっちりと本体がコントロールしている。そのうえで、納期を遵守し、品質、コスト削減、継続的な技術革新といった点で能力が高いと認められたサプライヤーだけに外部委託をしている。トヨタはサプライヤー企業と密に連携し、サプライヤーの問題には誠実に、お互いに敬意を持って対応してきた結果、驚くべき水準のプロ意識に基づく信頼関係を築き、品質管理を徹底できるようになった。
対照的にボーイングは、トヨタの多層構造のアウトソーシングのモデルの本当の価値や研ぎ澄まされた慣行は顧みず、表面的にトヨタの方式をまねた。その代わり、ボーイングは内容の薄い契約に基づき、納入期限を守っても報奨は無く、期限を守れないとペナルティーを課すという方法で、生産スピードが最も遅いサプライヤーに合わせたおかしな奨励制度を作り出した。
■海外移転のリスク
航空機のような複雑な製品を製造する際、国外へのアウトソーシング、つまり海外移転はある程度避けて通れない。ある部分のノウハウは外国にしかないということが起こりうるからだ。例えば、リチウムイオン電池の製造能力は米国外にあった。ボーイングはバッテリーを、海外生産に頼らざるをえなかった。787の構成部品の30%以上は外国製だ。対照的に747では、外国製の部品はわずか5%だった。
もちろん必要ならば海外移転をすることは原則的には間違っていないが、言語や文化の違い、延々と連なるサプライチェーンとの物理的な距離はリスクを高める要因となる。リスクを低減するには、サプライヤーと常に継続的な対話を続け、現場にも介入していくことが求められ、追加的なコストが発生する。ボーイングはこうした対話や介入を予定しておらず、追加的なリスクが顕在化してしまった。
■コンピューター頼みの対話
顔と顔を突き合わせ、現場で対話するよりも、ボーイングが選んだのはExostarというネット上のコミュニケーションツールだった。サプライヤーは日々、業務の最新の進捗状況を入力することになっていた。このツールでサプライチェーンは業務を可視化できるようになり、業務上の重要なプロセスの管理や調整が向上、開発にかかる時間とコストは抑えられるはずだった。人と人が直接対話する代わりに、コンピューター自体がリアルタイムで浮上した問題を提起してくれると想定されていた。
驚くことではないが、このツールは失敗に終わった。サプライヤーは、文化の相違や信頼の欠如もあり、正確にタイムリーに情報を入力しなかった。この結果、下請け企業もボーイングも、時機を得た形で問題を把握することができなかった。ボーイングがコンピューターを介した対話に依存したことは、全員が同じ情報を共有できるよう「顔を合わせて対話を継続」という記事とあまりにも対照的だ。
■労働関係のリスク
ボーイングがアウトソーシングや海外移転に熱心に取り組んだ背景に、シアトルの本社での難しい労働問題を回避したいという思惑がどの程度あったのか、確かなことは分からない。ただ、明らかなのは、アウトソーシングや海外移転の意思決定に従業員を関与させず、ボーイングの経営陣は機先を制する形で意思決定をしたということだ。この手法はかえって従業員の反感を買い、アウトソーシングの決定により労使関係は悪化、コスト増要因となるストライキを招いた。
■プロジェクト管理の甘さ
787プロジェクトにはこれだけのリスク要因が予測されたのだから、ボーイングが実績のあるサプライチェーン経営に基づくリーダーシップの体制を構築し、多様なノウハウを生かして広範囲に及ぶリスクを予測し、その軽減に乗り出すと期待するのが普通だろう。ところが、そうはならなかった。これは驚きだ。
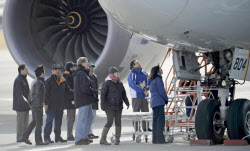
タン氏とツィンマーマン氏はある重要なケーススタディー(参考文献参照)のなかで、こう記した。「ボーイング787プログラムを当初率いたリーダーシップチームには、サプライチェーンのリスク管理の専門知識をもつメンバーがいなかった。従来とは異なるサプライチェーンを管理するのに必要なスキルがないため、ボーイングは海図を持たないまま、巨大な経営リスクを抱え込むことになった」
■手持ち無沙汰な経営陣
これまで述べてきたようないくつものリスク要因が重なり、ボーイングにとって現在進行形の脅威が顕在化している。では、こうしたリスクに直面しようとしていたころ、経営陣はどこで何をしていたのか? 最初に787型機の開発が決定した当時のCEO、フィリップ・コンディット氏への2011年のインタビュー(参考文献参照)を通じて明らかにしよう。
2001年、コンディット氏の指揮のもと、ボーイングは本社をシアトルからシカゴへ移した。この決定は後継者であるマクナーニ氏が引き継いだ。表向きの理由は、米国中に散らばるボーイングの各部署との距離の偏りを無くすためというものだった。インタビューでコンディット氏は別の理由も隠さなかった。経営者として同氏は「航空機はどうやって設計するのか」といったたぐいの面倒な課題や、シアトルにやってくる顧客(つまり航空会社)との退屈な会合がいやだったのだ。
本社移転のあと、コンディット氏はシカゴのビジネス界の人たちと多くの時間を過ごすようになったそうだ。そこで彼は、「CEOたちが頻繁に集まって、新しい企業の上陸から世界的規模の公園の建設まで、都市の今後について決定を下していくのを目の当たりにした」。「私はこんなにいろいろなことが起きているのかと驚いた」とコンディット氏は語った。「スターバックスやマイクロソフト、コストコ、ボーイング、ウエアーハウザー、その他いろんな小さな企業が一堂に会する会合なんて、シアトルではめったにない。それがシカゴではいつも行われている」
こうして、ボーイングのCEOがシカゴで、ボーイングの将来の戦略を練ったり、他社のCEOたちと都市の今後について議論を重ねたりしていたころ、シアトルの経営幹部たちは「いかに飛行機を設計するか」という面倒な、しかし会社を揺るがしかねない経営判断をしていたのだった。
Steve Denning, Contributor
(c) 2013 Forbes.com LLC All rights reserved